Part of the LCR4.0 project – the Virtual Engineering Centre worked together with GenLab to explore how their existing factory layout and current processes could be optimised to improve efficiency and meet growing customer demand for their products without compromising their handcrafted approach or having to make greater financial investments.
Opportunities for the adoption of digital innovation included the use of industrial internet of things for preventative maintenance, to explore improved connectivity of products and how the current factory layout and manufacturing process could be changed to improve productivity.
Working with Genlab, the VEC studied the existing floor plan and factory machine layout, evaluating process times at different work stations. Using this high level production data and layouts, the VEC created a full model factory simulation using specialist software, SIMIO. The results enabled Genlab to explore alternative layouts, helping them to understand which layout gained maximum efficiency.
Download Case StudyThe support meant that GenLab could:
- Focus and validated ambitions
- Achieve business growth
- Explore new possibilities without risk
- Achieve 20% increase in productivity through the factory simulation
- Improve assembly time by 30 minutes
- Increase capacity by 20% with no added investment or automation
Client opinion
"Working with the VEC has introduced the company to a no-nonsense approach to adopting new digital tools as a means to improve productivity. With the VEC’s support, Genlab is excited to explore how Industrial IoT & Virtual Prototyping can further help us create a new generation of products and to better meet our automotive and industrial clients demand."
Phil Crompton,
Finance Director
GENLAB
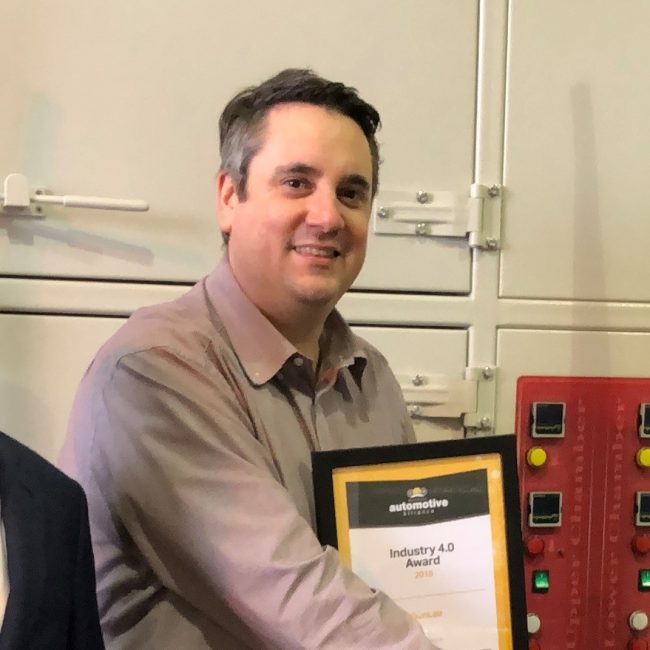